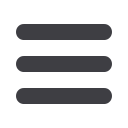
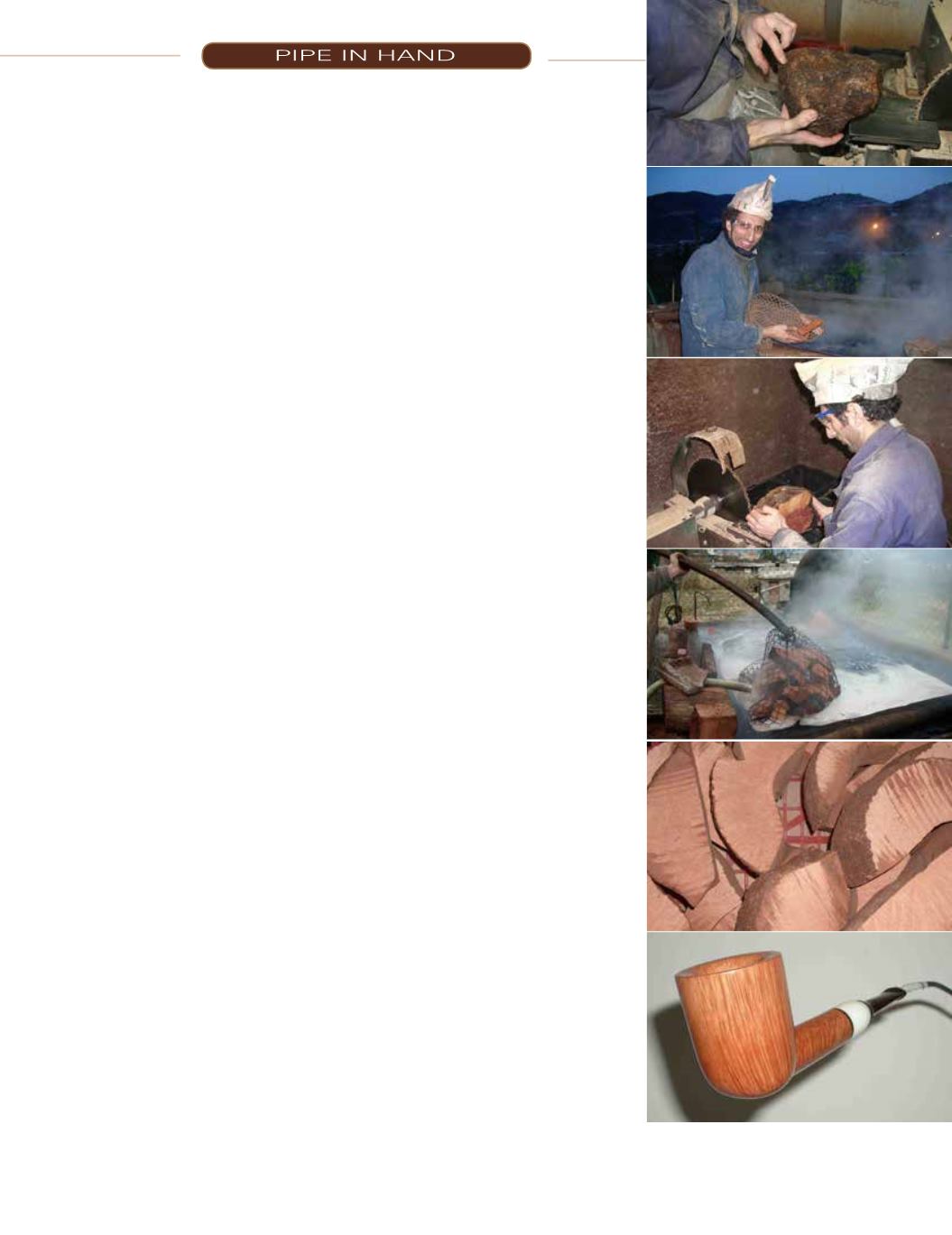
38
TOBACCO BUSINESS INTERNATIONAL
JULY/AUGUST 2015
I
met the charismatic Romeo
Domenico, also known to his friends
as “Mimmo,” at the Cigar and
Tobacco Fair in Frankfurt, Germany this
February. I was fascinated to learn about
his family’s history in producing some of
the finest briar in the world.
Romeo Domenico’s father, Filippo (or
“Pippo”), and his two brothers learned
how to cut briar in 1946 in a large briar
factory called Surfaro e Gulli in southern
Italy.After working there for several years
with his uncle Vinci Domenico, Pippo
decided to try his own luck. He moved to
northern Italy, eventually settling in the
village of Taggia in 1969. The business
he started there, which is now led by
Mimmo, would come to include eight
briar cutters.
Briar Basics
Briarroots are found in wooded
areas around the Mediterranean, often
growing next to cork oaks. The briarroot
should be at least 20 years old to be ideal
for pipe making—some are even older,
up to 100 years.
When the roots are harvested, they are
often kept in the soil in order to keep them
moist before transportation. After the
roots arrive at the cutting factories, they
are also stored underground and watered
every day to maintain their relatively
high level of moisture. Cutting the briar
is a lot like cutting fine diamonds; it
takes an expert’s eye to evaluate what is
hidden within each individual block and
get just the right size and shape out of it.
To be a good cutter, you also have to be
very careful of your fingers, according to
Mimmo.
Each cutter goes through close to
1,000 pounds of briarroot a day, grading
the quality of the wood (depending on
the structure of the wood, flaws, etc.),
using up to 20 different international
standards for sizing, and finally selecting
which cut to use—whether it’s plateau
or ebouchon for bent or straight pipes.
Finally, Mimmo personally judges the
quality of each individual block of briar.
After the briar blocks are cut, only about
30 percent of the wood makes it to the next
level of being boiled for 10 to 12 hours to
eliminate any foreign live matter before
being dried.The drying process takes several
weeks and is quite important; thewoodmust
be exposed to conditions that are neither too
humid nor too dry.This involves moving the
blocks around, depending on the stage in
the process. Mimmo believes his attention
to detail in the drying process is part of the
secret to his success in producing superior
briar blocks.
Today there are only approximately 12
briar makers around the Mediterranean
area and all are small businesses
employing from one to five artisans
as cutters. Finally, Mimmo points out
that briar is a very challenging wood to
process. Tere are other types of inferior
wood that are much easier to deal with,
but personally he is very happy that
briar is both complicated and hard to
manufacture—the resulting pipes are
worth it.
TBI
The Romance
of
Briar
By Erik Stokkebye